Supply chain telemetry: good idea or bad call?
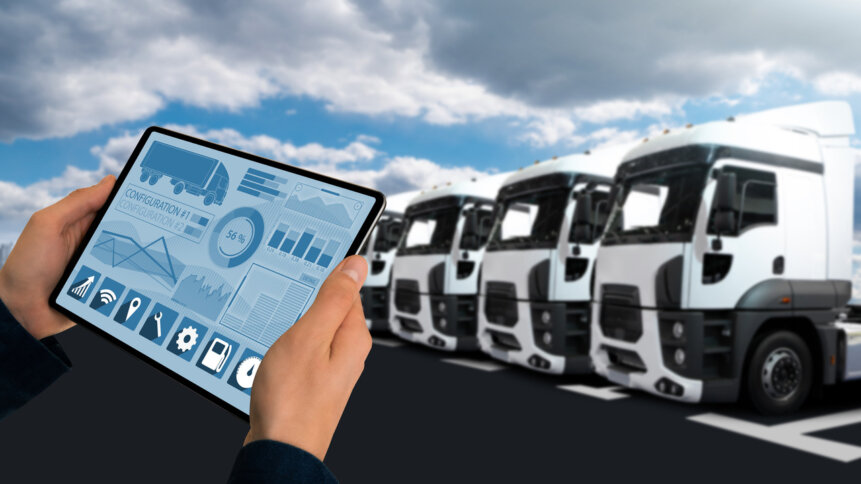
Supply chain telemetry: good idea or bad call? Like most complex questions on which industries, jobs, and economies hang, the answer will very much depend on who gets asked the question. As a technology, it’s responsible for delivering last mile delivery tracking, which has revolutionized expectations throughout the supply chains of the world. But can it also be the company spy you carry with you, wherever you go?
What is telemetry?
First of all, it’s worth defining our terms. Telemetry is the collection and use of data about a process through sensors that monitor that process as it happens, and feed into an overall picture. Most typically in supply chain telemetry, we’re talking about vehicle telemetry, but there are other types of sensor data in the supply chain, too, like warehouse telemetry, to track everything from warehouse picking speed to cold store temperature.
Any set of data tools that feed into the overall picture of a supply chain, its resilience, its vulnerability, its quirks and strengths and weaknesses, is part of the equation of supply chain telemetry.
So it follows from first principles that there’s not going to be a smooth, simple answer to the question of whether supply chain telemetry is a good idea or a bad call, because sensors that track one kind of data will provoke an emotional response from some people in the process, while sensors that track a different data point will barely raise an eyebrow.
For instance, nobody’s likely to feel it’s a mark of corporate mistrust if the cold store at a warehouse has an IoT (Internet of Things) sensor that measures temperature fluctuations to ensure that the cold store is always kept at the correct temperature for optimum meat storage. Whereas, by comparison, truck drivers required to carry a sensor for last mile delivery tracking might well feel aggrieved by the presence of the technology, and as though the company trusts the sensors more than it trusts them to do their job.
More is probably better.
In the world of data management, generally in the 2020s, the trend is towards bigger and more detail-rich data as a matter of course. The more data you have, the more you have to do to manage that data and extract value from it, certainly, but if you don’t have the data in the first place, you can extract the square root of zero from it – while your competitors are making data-driven decisions and pulling ahead.
As such, companies that operate in a supply chain will tend towards gathering more and more data from every nook and cranny of their process, because the maxim exists that even if you don’t currently know the value of the data you own, you might one day realize both what you have and its relative value if it allows you to unlock new levels of data-richness, functionality, or assessment, or if it allows you to deliver more value to your customers or your part of the supply chain.
Lines of debate.
Focusing particularly on the vehicle telemetry section of the supply chain helps illuminate the lines of debate on the relative goodness or badness of supply chain telemetry.
On the one hand, vehicle telemetry takes the business of transportation to a whole new level of data-richness, and has transformed what is possible within the supply chain. It allows for the precise ETAs (estimated times of arrival) that power 21st century “just-in-time” deliveries and relatively seamless linkages in the supply chain.
By showing the journeys actually traveled, it also allows for more effective fuel supply and provisioning, as well as the gathering of data on the most effective routes (which are not always the shortest A-B routes – because both human instinct and the legacy systems designed by humans have a tendency to rely on those straight-line routes, which means they can easily become clogged hotspots, as everybody gets the same information and heads for those direct routes).
The data supplied by vehicle telemetry can deliver better routing, better fuel economy, less pollution, less stress on drivers, and crucially of course, those data-rich connections in the supply chain that, for instance, enable the kind of last mile deliveries within precise windows of time that have become the most fundamental characteristic of the modern supply chain. If the data is used effectively by an integrated system and an intelligent fleet manager, vehicle telemetry can be an investment that revolutionizes what the supply chain can deliver, and what it can expect.
Finding the downside.
So… where’s the bad?
Well, the bad comes from the way in which vehicle telemetry has been used in the past as a proxy for human worker telemetry. It’s fine to track vehicle wear and tear, to streamline fuel usage, and to deliver route optimization to drivers – all those elements track material resources of the company, and feed in the data to an overall picture of the supply chain, so that it can be as effective as modern technology allows.
Previously though, companies have weaponized vehicle telemetry into a kind of vehicular spy, so that drivers have been penalized based on the telemetry’s records of their deviation from routes, or their personal use of the vehicle, both on and off company time.
While for the most part, such punishment of drivers belongs to an earlier era of vehicle telematics, it has left a historically bad taste in the mouth of many, and even though most modern delivery fleets see the benefit in being a human being about drivers using their vehicles for necessary non-work trips, the fact that the telemetry in the vehicle can be used to locate drivers in particular places where their work gives them no need to be has created a sense of inherent mistrust of the technology in a generation of drivers that feels unlikely to be easily dissipated.
Humans – more than resources?
Ironically then, the notion of vehicle telemetry being a bad call has two strands to it. In the first place, by monitoring the movement of drivers, it can be said to bring the drivers down to the same level as fuel and lug nuts – a corporate resource, the movement of which the company feels a perfect right to monitor.
While there’s technically an element of truth to this, no-one wants to feel like a human resource, or to be devalued to the point of equality with inanimate objects – it’s a bad way to build team morale and personal buy-in from staff.
The Star Trek Lesson.
And in the second place, there’s the anodyne truth that allows us to deliver a smoothed-out overall verdict on whether supply chain telemetry is a good idea or a bad call.
It’s neither.
Supply chain telemetry is a hunting dog, with data as its prey. It’s a tool that has no inherent moral value. It becomes a good idea when it’s used by companies in the spirit of improving safety, reducing driver stress, and delivering loads to tighter deadlines without imperiling the human in the search for speed.
It becomes a bad call when it’s used to unfairly punish drivers for their actions, to cut margins to the bone, or to add stress into the supply chain by negatively incentivizing drivers to take risks to meet the expectations of software.
Supply chain telemetry enables the world as we’ve come to understand it in the last ten years – a world that saves money by delivering within tight time-windows, that improves customer service and customer confidence that when companies say a delivery will be there at a certain time, it absolutely will be. The world of last mile delivery tracking for certainty and profit.
It also has a history of increasing stress in the workplace by tightening performance targets. That means supply chain telemetry is neither wholly a good idea nor a bad call. Its moral value and impact depends on the morality of the people who invest in it, and the uses to which they put it.
So perhaps the question is best answered by a re-framing of the idea. Human beings who use supply chain telemetry – good idea? Or bad call? Only time will tell.