Digital twins deliver business intelligence masterclass
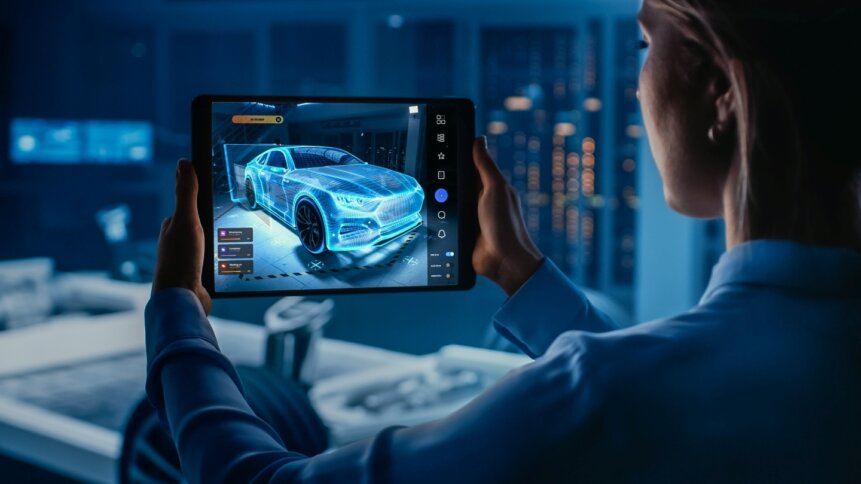
Digital twins give users a treasure trove of operational insight. The benefits can be applied across a wide range of activities from space exploration (NASA was an early pioneer in digital twins) to seabird surveillance. And mainstream adopters of digital twins are industrial users. The transformative information derived from real-time data and generated by industrially relevant models can translate into millions of dollars in savings for firms. And the best way to find out how digital twins are impacting industry is to dig into some practical examples.
To prime the discussion, let’s begin by answering a key question – what is a digital twin? Digital twins are virtual copies of the real world. These digital replicas of real-world assets can be pictured as supercharged simulations fed by an array of live-streamed data. Gathering this wealth of information are potentially millions of sensor nodes unified by Industrial Internet of Things (IIoT) architecture, with measurements stored securely in the cloud. Unifying the data helps with information access and provides a single source of truth for users.
Digital twin design
Looking into the design of digital twins more closely, data accuracy and provenance are critical. To avoid everything going GIGO (‘garbage in, garbage out’) operators need to have confidence in their data. And solutions such as GE’s SmartSignal provides sensor health coverage to ensure that operational technology (OT) data sources are within bounds and performing as expected. Dubbed Predix, GE’s digital applications (which includes a range of digital twin blueprints) sit upon a shared IoT edge-to-cloud platform that leverages Amazon Web Services (AWS) to enable secure processing and analytics.
Ahead of deployment, operators can use tools such as the Oracle IoT Digital Twin Simulator to test that all’s good in terms of applications and analytics. Virtual software-based sensors can be turned on and off and set up to provide alerts and realistic event details. Validating the design of digital twins using simulated end-points early on can save time further down the line. And if measurement devices are hard to access in the real world, engineers will certainly be glad to have this option.
The computing eco-system supporting digital twins runs deep. Rescale – a firm helping users take full advantage of high-performance computing in the cloud – recently announced a partnership with NVIDIA to extend GPU-enhanced digital twin performance on its platform. And NVIDIA’s Chris Lamb is buoyant about the prospects, noting rising demand for virtual representations of products and processes. “The realization of the industrial metaverse will have a profound impact on the design, performance, and supply chains of physical products we use every day,” he commented at the time of the announcement. “Our customers increasingly use AI and digital twins to design better products and optimize how those products will be manufactured.”
Vendor support
Supporting these breakthroughs directly are a raft of digital twin software vendors. And it’s clear that providers have made great progress in taking much of the heavy lifting off the shoulders of users. The result is that building a digital twin today is much less taxing than in the past. Depending on users’ needs and experience, building a digital twin can be as simple as dragging and dropping icons on the screen. And modern packages such as Ansys Twin Builder give users easy access to incredibly detailed engineering models for quickly creating connected replicas of in-service assents.
Starting at the model build stage, users can deploy, validate and examine the runtime capabilities of their digital twins to prepare the ground for day-to-day virtual operations. On a project basis, the rewards of digital twins can extend through the whole operational lifecycle. Great examples can be found in architecture, engineering, and construction (AEC), where modeling can help to determine building compliance, checking access, and other requirements before breaking ground.
“A digital twin offers a means to test ‘what-if’ scenarios, including the impact of design changes, weather disruptions, and security events,” writes AutoDesk. “It collects substantial data under one environment.” Digital twins can inform facilities management to optimize heating and cooling as well as identifying efficient maintenance schedules. In fact, pre-emptive servicing of equipment is one of the big rewards of digital twins. And improvements in materials and sensing technologies are adding to operational savings by better informing predictive maintenance and reducing unplanned downtime.
Offshore applications
Microsoft, which offers a range of tools designed for digital twins through its Azure platform, is – together with partners – pushing the technology into new territory. Building on the success of a pilot project off the coast of Scotland – which combined AI, machine learning, and image recognition to count puffins – experts are expanding their habitat monitoring efforts. The clients (in Scotland and, more recently, in The Netherlands) are both wind farm operators. Firms want to demonstrate that renewable energy generation can coexist with nature. “By conducting large-scale research into the effects of wind farms on the surrounding ecosystems, and by making the vast quantities of data available in a public platform we can facilitate research and collaboration in a simple way,” said Dennis Breugelmans, Project Director of International Markets at SSE Renewables. “We can learn in real time how to limit and avoid negative impacts, whilst promoting the positive ones.”