Crop harvesting robots dream of soft fruits
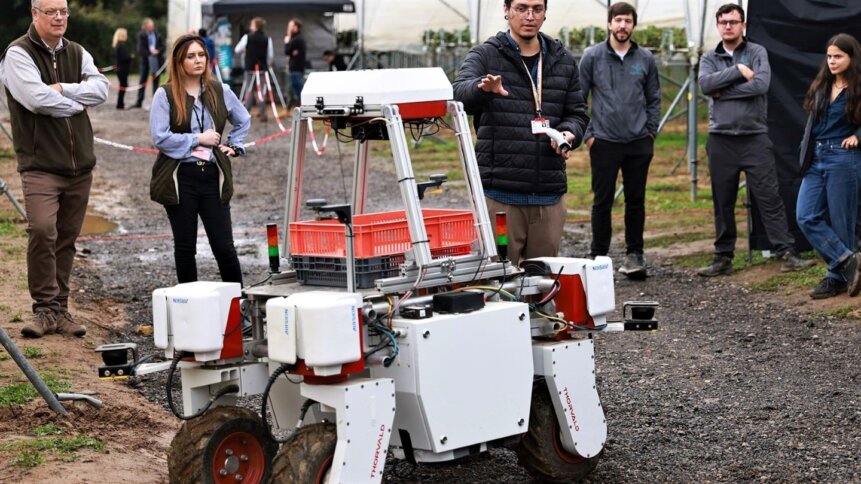
Picture a summer’s day. You’re strolling through the countryside; looking out across acres of fields. What do you see? In temperate regions, there’s a good chance that you’ll notice some polytunnels – plastic-covered greenhouses that provide favorably hot and humid growing conditions for fruits and vegetables. And then, if you were curious to peek inside, there’s a possibility that you’d find not people, but crop harvesting robots patrolling up and down.
Projects such as Robot Highways – a futuristic vision of soft fruit farming being developed in the UK – are adding to the increasingly automated world of agriculture. The program, which kicked off in 2020 and is planned to run for five years, features a range of partners. Telecoms firm BT announced this week that it delivered edge and cloud architecture to help the crop harvesting robots to interact and cooperate. At the heart of the system are multi-functional autonomous units supplied by Saga Robotics of Norway.
Modular design
The firm’s crop harvesting robot technology – which was spun out of the Norwegian University of Life Sciences (NMBU), situated near Oslo – can be configured to operate not just in polytunnels, but also on open fields and vineyards. As the developers explain, the battery-powered robots provide up to four-wheel drive and four-wheel steering with passive suspension to maintain good traction across rough terrain. Research notes indicate that designs feature a local Ethernet as well as CANopen data channels – cars, boats, aeroplanes, and even some coffee machines include controller area network (CAN) architecture.
Named Thorvald II, the crop harvesting robots contain an onboard computer running Robot Operating System (ROS) – a set of software libraries and tools that help developers build robot applications – on Linux Ubuntu. In the Robot Highways project, all this technology is put to work to automate and streamline soft fruit farming. Taking strawberries as an example, fruit picking can be laborious work. In fact, pickers can spend a third of their time carrying boxes of strawberries from the plants to weighing stations before storage. To ease the burden, trains of crop harvesting robots can shuttle the ripe fruit around the farm.
Also, the Robot Highways project is not just about picking. Fitted with UV-C emitting hoods that arch over lines of crops, robots can move back and forth shining specific wavelength bands of light onto the plants (at night when it’s most effective) to protect against powdery mildew. Live data transfer is enabled over 4G/5G – hence the involvement of telecoms partners – to a central control system, which can provide remote support and optimize treatment.
Google likes strawberries too
The business case for strawberry crop harvesting robots appears to be a compelling one. X Company, which started life as Google X and now sits as a subsidiary of parent firm Alphabet, is also examining how technology can be deployed to select only fully ripened fruits. Staff at the firm have been photographed conducting research in strawberry fields in Northern California, US. Dubbed, Mineral, the project uses a high-tech ‘plant buggy’ to count, classify, and image not just berries – as it turns out – but a whole range of crops from melons through to oats and barley – across the growing season.
Building on the progress made by sister firm Google in mapping the Earth, X Company is combining the detailed photographs gathered by the plant buggy with other information such as satellite imagery, weather data, and soil information. According to the team, the plan is to create a full picture of what’s happening in the field and use machine learning to dig into how plants grow and interact with their environment.
See and spray
The Robot Highways team and Alphabet’s X-Company are by no means the only groups developing robots capable of working in the field. In the US, Blue River Technology – acquired by agricultural machinery giant John Deere five years ago for $305 million – has revolutionized the way that farmers treat their fields. Dubbed ‘See & Spray’, Blue River Technology uses AI to identify which areas to spray using nozzles towed behind a tractor. It’s estimated that at least 1 in 10 lettuces grown in the US benefit from the technology, which in this case helps to thin the crop so that lettuces are able to grow evenly. In the past, farm workers would have to laboriously walk up and down the field picking out shoots – the ground is initially overseeded to make sure that no patches are bare, to maximize crop coverage.
Targeted spraying dramatically reduces the quantity of chemicals that need to be applied. Electrification, as with the Robot Highways project, is also playing a role. By 2026, John Deere (owner of the ‘See & Spray’ technology) will introduce a range of zero-emission electric and hybrid-electric solutions to its vehicle fleet. This includes models not just for the agricultural sector, but also 20+ electric and hybrid-electric vehicles for use in the construction market.
In December 2021, John Deere agreed to acquire majority ownership of Kreisel Electric – an Austrian developer of high-density, high-durability electric battery modules and packs. Looking into the product details more closely, it’s likely that crop harvesting robots won’t be the only electrically powered equipment operating in the field. Turf management vehicles, small tractors, and compact construction vehicles also have the potential to rely solely on batteries as a power source.