Warehouse safety takes a front seat thanks to new tech
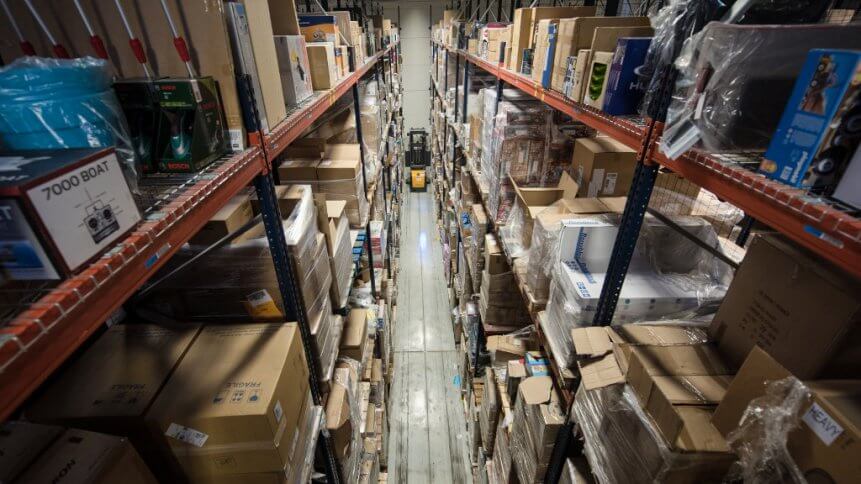
One of the biggest dilemmas faced by warehouse managers and facility businesses is the issue of safety. Especially as many industrial businesses resume regular operations after a global pandemic, warehouse operators need to be particular aware of staff safety concerns.
Infections might be a new concern following the events of last year, but safety concerns have always plagued the warehouse sector – one of the reasons that fully automated warehousing would appeal to business owners, despite the potential impact to human workers. In fact in 2019, the U.S. Bureau of Labor Statistics showed that 4.8 out of every 100 workers recorded injuries in the warehousing sector that year.
Fortunately newer technologies are constantly being innovated, and the warehouse safety space is not being overlooked for these crucial concerns. Today TechHQ takes a look at some of warehouse safety measures driven by technology that are already available in the market. Not only do they make the facility safer, but in some instances enhance the efficiency of day-to-day operations as well.
Warehouse management system emphasizing safety
Now warehouse management systems (WMS) come in all shapes and sizes and are widely relied upon to manage any business with storage and logistical needs of a certain scale. However, these can vary greatly in application and scope, and some businesses might even see a WMS as additional expenditure for just managing stock.
While that might eb the primary purpose, newer WMS’ also enable the control of a variety of on-floor systems, operational technology, IoT sensors, and can even integrate with a range of personal smart devices for the staff. So in addition to tracking inventory, data could also be transmitted to autonomous robots and transportation equipment, particularly for the more hazardous jobs such as heavy lifting and going into precarious spaces.
These machines and data can help reduce the number of people being put in risky situations due to a lack of an alternative that is safer. WMS data can also help companies assess how many people are required for future hazard duty, and which can be handled by automated systems.
Traffic management systems
Bigger facilities might have floor space and outdoor areas that are not easily covered on foot, not forgetting the moving products from A to B, onsite transportation needs, and offsite distribution such as shipping and cargo vehicles. For a warehouse to work efficiently, these systems should work in harmony with as little friction, and as little danger to employees, as possible.
They also don’t have to highly advanced systems – simple traffic management solutions can be deployed and integrated without causing too much disruption or requiring substantial oversight. AI and other technology can help determine the correct distances and dimensions of space need to avoid collisions and overcrowded bottlenecks.
Another simple, elegant method is to implement a one-way travel system. This can be assigned by a WMS that has done the necessary calculations to determine the best, safest routes for both people and machines – or it could even be a lights- or sensor-based method that identifies which spaces are blocked or congested, and which areas are safe to travel, even while operating distracting heavy machinery.
And sometimes, just plain and simple floor markings might do the trick to designate parking and pedestrian zones and to manage traffic and personnel flow, ensuring they don’t clash.
Guided forklifts
Speaking of heavy machinery, forklifts are an essential tool in many warehouses, helping to manoeuvre goods efficiently and quickly. Forklifts are also involved in the most common types of accident in the warehouse, not just endangering worker safety but even responsible for 90% of pallet damage accidents. Even worse, forklift truck accidents are the number one cause of fatal accidents on the floor.
OSHA data shows that more than 40% of fatalities are caused by forklift overturning or tipping. Physical guides such as solid steel end barriers can actually be surprisingly effective at cutting down dangerous forklift incidents, but a more proactive solution would be implementing proximity sensors, that would emit an alarm when too close to people objects – a shrill alert could provide the driver with the valuable time to anticipate the danger and avoid any collision.
There are more advanced, automated systems as well. Low-powered lasers can be embedded into walls and vehicles themselves to detect the forklift’s proximity to objects, sounding an alarm or even automatically engaging brakes or performing emergency manoeuvers to avoid collision.