Productivity gains from automation hardware begin with software
Few industries remain untouched by technology. Manufacturing automation has a long history, dating back to the industrial revolution. Automation and technological advances have always driven the sector and it’s often the first vertical to embrace the newest and most powerful breakthroughs in technology and hardware.
Long before technologists began talking about IoT, for example, manufacturers were controlling and attenuating their systems and machinery. And to this day, the sector is considered a place where new practices are explored and utilized in a drive for efficiency, increased output and improved quality.
Manufacturers do not pursue that spirit of innovation from a sense of adventure; rather, it’s an integral part of remaining competitive in a sector where excellence in the automation of processes and machinery distinguishes one manufacturer from another. The degree to which technology and today, robotics, are successfully implemented differentiates a market leader from an also-ran.
Whether it’s pioneering the technology behind digital twins or predictive maintenance, robotics, and automation specialists are helping manufacturing production lines produce more, of a better quality, at a lower cost. Plus, in certain sectors with specific sensitivities, work is carried out more safely, more hygienically and with a smaller carbon footprint.
The component parts
In most people’s minds, robotics is likely represented by images from a German or Japanese automotive manufacturing plant from the 1970s or 80s. But the arresting images of large, industrial robots spot-welding or assembling high-end vehicles was only a part of the picture then – now, the so-called “back end” of robotics plays an even greater role, usually unseen by visitors to a busy facility.
The associated software and supporting hardware play their roles on the factory floor and back office, as does another unseen element: the project planning and consultation that goes into every successful implementation of automation. Increasingly, much groundwork is achieved in a computer simulation in an automation project’s initial stages. Software continues to play a pivotal role in machine control, digital modeling of processes, predictive analysis, and quality attenuation.
The robots march: the manufacturing factory floor from 2023
Pre-project innovative software deployment can lower the risks inherent in deploying automation systems, but short-term client contracts and unpredictable costs outside of direct control (such as power costs, currently, for example) can urge decision-makers to remain conservative regarding automation and robotics.
That reticence is understandable, but it’s not entirely warranted. Today’s automation systems can be built entirely modularly, deployed piece-by-piece in areas where the fastest “wins” are. Additionally, companies can keep their future options open by carefully choosing open-ended solutions in both hard- and software. As new markets emerge and existing demand changes, the best automation solutions adapt and scale for growth.
The keys to this scalability and elasticity in automation & robotics consist of a surprisingly few components. Paramount is the consultative supplier of automation systems, that will assess the business case for automation in addition to the operational details. Companies that have existed in the sector since the last century have developed a credible reputation in this respect. (The analog in the technology sector would be IBM – still going strong decades after the computer revolution.) In manufacturing and engineering automation, the experience and broadly-skilled capabilities are best found in companies like KUKA Robotics, a company that celebrates its 125th anniversary this year.
In addition to supplying best-in-breed automation hardware, the company is a known leader in technology specific to this sector. Its software, electronics, and supporting hardware are tuned to automated systems on the shop floor of household-name companies worldwide (you can read some typical case studies here).
In recent years, the popular buzzword used around robotic automation was cobots, a portmanteau of ‘collaborative robots.’ Originally designed to work safely alongside human operatives, there were, in truth, very few applications where cobots were viable. Today, the talk is of ‘cooperative robots.’ These are much easier to set up and control, and have user-friendly GUIs like iiQKA, the latest operating system from KUKA installed on its LBR iisy range. The emphasis with the latest generation of automation is very much on users reaping efficiency rewards faster.
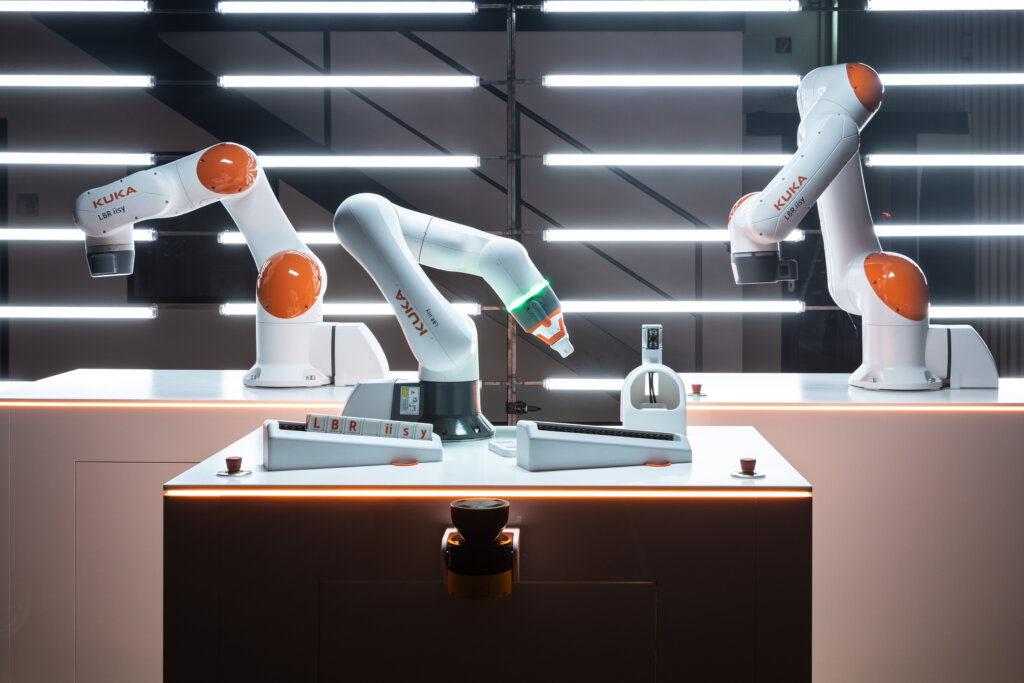
Source: KUKA
KUKA Robotics
Operationally, the benefits of automation come in the form of better quality control, increased output and efficiency, and predictable and reliable equipment. Most companies will expand their automated systems in as controlled a manner as possible to reduce risk and ensure implementation costs don’t spiral. In 2023, that process can begin entirely in software – such are the benefits of a technology-focused partner like KUKA. Proposed systems can be modeled in digital twins and then implemented in a controlled and highly-scrutinized way.
In this manner, operational interruptions are minimized, and the business benefits can be measured from day one of implementation. ROI begins early because, as well as the expertise in automation that KUKA brings to the table, its years of experience in the sector are brought to bear on any situation. Users can also monitor the performance of their assets, access technical information and get around-the-clock support from a digital portal.
Production systems and manufacturing methods are, by nature, slow to change, so any decisions on automation made today must be adaptable and scalable for the future. The ethos of KUKA Robotics is on systems tuned to a company, as well as for specific purposes. Therefore all operational and business process improvements are made with an eye on adaptability and are planned and executed with a significant weight placed on future-proofing.
To find out how automation anywhere in the enterprise’s manufacturing, production, or engineering functions can be made significantly more effective, contact an expert for an initial consultation