Finding Nemo’s Garden with the aid of digital twin technology
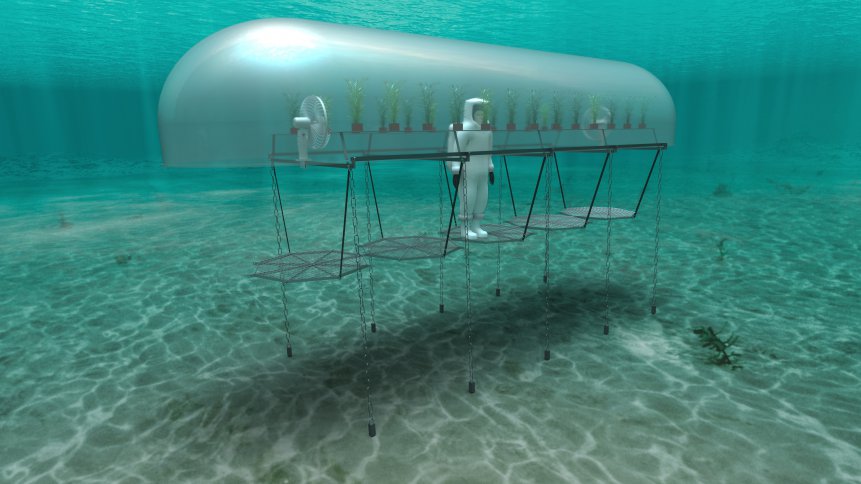
Digital twin technology has been gaining popularity around the world across numerous industries today. While it was initially designed for only specific industries, digital twin technology can now be applied to almost any connected industry.
The most common use cases for digital twin technology include monitoring the maintenance of machinery and equipment in the oil and gas industry as well as the manufacturing industry. Now, digital twin technology is also being adopted in the healthcare industry and even for supply chain monitoring.
Another interesting industry where the technology is expected to make a difference in the agriculture industry. The agriculture space is heavily in the process of adopting more technologies to boost its output to meet global demands.
In an effort to innovate cycles and scale crop yields, Siemens Digital Industries Software has deployed its Xcelerator portfolio of software and services to shorten innovation cycles with Nemo’s Garden, a startup focused on sustainable underwater cultivation of corps.
Founded in 2021, the Nemo’s Garden team of engineers, divers, and scientists have been working to prove the viability of cultivating herbs, fruit, and vegetables underwater. Nemo’s Garden’s key innovation, a sub-aqua biosphere, is a unique type of underwater greenhouse, able to harness the positive environmental factors of the ocean – temperature stability, evaporative water generation, CO2 absorption, the abundance of oxygen, and inherent protection from pests – to create an environment ideal for crop cultivation.
However, the team has been facing some challenges, especially with harsh winters, short summers, and initial seafloor-use permit limitations. The challenges capped Nemo’s Garden to one growth cycle a year, which has meant only one innovation cycle per annum. Design changes, lengthy physical testing, and heavy manual monitoring processes during the growth cycle led the Nemo’s Garden team to seek out ways to speed up their innovation and scale the operation.
As such, the team decided to work with Siemens, leveraging the Xcelerator portfolio of software and its services to help Nemo’s Garden get to the next stage of development and get prepped for industrialization/commoditization.
According to Luca Gamberini, Co-Founder, of Nemo’s Garden, “we have seen benefits in understanding the flow of water around the shapes of our biospheres. We have a greater understanding of the points of stress on the structure around the biospheres. We also understand how the different interactions of solar radiation, the temperature, and all the physical factors, act on the plants. All thanks to the ability of the digital twin to replicate our system.”
A comprehensive digital twin of the Nemo’s Garden biosphere has been built that encompasses not only its design evolution using Siemens’ NX software but also enables simulation of the growing conditions within it, the impact of the equipment on the body of water, as well as the full environment in which they are installed – all accomplished using Siemens’ Simcenter™ STAR-CCM+™ software.
Hence, the Nemo’s Garden team is no longer limited by weather conditions, seasonality, and short growing seasons or limitations on diving and monitoring. Adaptations to the biospheres can be tested in the virtual world, enabling the team to refine the design at a massively accelerated rate.
Siemens was also able to train a machine-learning algorithm to monitor plant growth as well as the environmental conditions within the domes for Nemo’s Garden. When this algorithm is deployed onto Siemens’ Industrial Edge computing devices in each biosphere, the plants can be monitored via a cloud-based dashboard throughout the season, from anywhere, in real-time.
These Industrial Edge devices will be connected to actuators – to automatically adjust air circulation, humidity, irrigation, and nutritional dosing throughout the whole season. This will be the foundation of a global agricultural service, optimized for subsea operations and attuned for each of the world’s oceans.
“Digitalization isn’t only for big companies, it is for all companies. In fact, great gains can often be realized in smaller or start-up companies. The work we do with startups can amplify the impact they have on the world, aiding in and speeding up innovation,” said Eryn Devola, Vice President of Sustainability, Siemens Digital Industries Software.