How 3D printing is transforming the production line

Now available to suit the budgets of small startups and large players alike, 3D printing has begun to break the mainstream. The process, known formally as additive manufacturing, comprises joining materials to make objects from 3D model data.
The most common method— and what we have in mind when discussing 3D printing— is extrusion, where a polymer rod or filament is heated, melted and forced through a nozzle in the print head.
A layer of polymer is deposited in a prescribed pattern, resulting in a freestanding 3D object. The relatively simple concept— behind the increasingly complex and advanced machinery and software— is being embraced by the manufacturing sector.
3D printing for prototyping
Unlike ‘traditional’ manufacturing methods which require expensive and specialist machinery and techniques— such as laser cutting, CNC milling, turning, and precision grinding— 3D printing allows for designs to be rapidly turned into physical objects in much less time and at far less cost.
The versatility and efficiency this offers have seen 3D printing rapidly adopted in industries such as aerospace, construction, industrial goods and automotive.
Given the low investment and rapid production time, one of the technology’s key applications is in prototyping. Here, 3D printing can allow manufacturers to tangibly showcase a prospective concept with highly complex geometries, and get instant feedback on design and functionality.
Research by Sculpteo found that this was the most common use case for more than half of 1,000 professionals deploying the technology across industries. Just last month, for example, Ashley Furniture announced it had deployed two SLA 3D printers on the factory floor, where it produces 300,000 pieces of furniture each week.
“It gives us the ability to quickly adapt to any suggestions or to any needs that we have, and create geometries that we’re not traditionally able to manufacture or machine,” Production Engineer, Brian Konkel, told 3D Printing Industry.
World-class sportswear brand Nike has used 3D printing to prototype and manufacture the 2012 Vapor Laser Talon football shoe for American football players. Similar products could soon be available to mainstream consumers, such as for prototyping a pair of custom glasses.
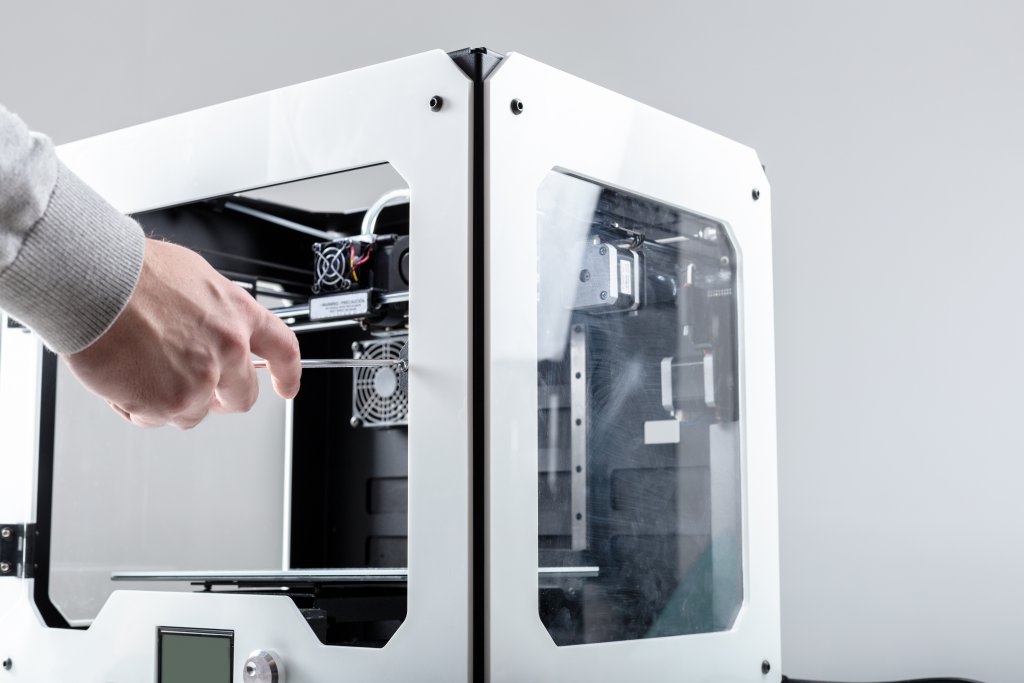
Designer working with a 3D printer. Source: Shutterstock
3D printing custom tooling
One of the earliest applications of 3D printing and one that is now widely used is that of custom tooling.
German automobile maker Volkswagen has been making use of 3D printed custom tooling since 2014, producing components for use on the assembly line. Negating the need to order the creation of specialized tools with a long wait time, this approach has slashed the cost of tool development for the firm by 95 percent.
The maker of Ford, General Motors also claimed to have cut the cost of one tool by nearly 1000 percent since 2015, while last month TechHQ reported how beer maker Heineken had turned to the technique to reduce the cost of a tool by 70 percent in Spain, as well as using the process to replace parts of machinery.
YOU MIGHT LIKE
3D printing is finding its place in enterprise
3D printing in production
3D printing is not limited to experimentative prototypes and custom tooling, however. For 43 percent of manufacturers, the process is allowing them to push new boundaries in production itself.
Now in more mainstream use, more specialist pioneers of additive manufacturing on the production line include Swedish supercar maker Koenigsegg, whose One:1 car utilized a number of 3D printed components in 2014.
In the world of Aerospace, Boeing’s 787 Dreamliner contains 30 3D printed parts. Construction of the RAF Eurofighter Typhoon also comprises additive manufacturing, while the USAF and Israeli Air Force also claim to have used the technology.
While automotive and aerospace industries are still driving much of the uptake of 3D printing, a report entitled 3D-Printing Trends 2019 by 3DHubs this year revealed that the combined might of SMEs made them the biggest users of the technology in Europe.
“Today, prototyping and small-scale production with 3D printing is standard practice for many engineers and designers in different disciplines,” said 3DHubs.
“After years of experimentation, industrial users are only now making their first steps towards full-scale production with Additive Manufacturing.”
Rather than investing in the technology on-site and CAD 3D software and skillsets, the report found firms were using remote printing services, allowing them to work on-demand with partners on custom designs.
3D printing future potential
Much like the adoption of other emerging technologies— such as artificial intelligence and augmented reality— the capabilities and use cases of 3D printing will soon be limited only by creators’ imaginations.
As it becomes yet more advanced and accessible— having seasoned in factory settings— 3D printing will likely see more consumer-facing usage, beckoning a new era of instant personalization in the retail industry.
In the world of fashion, for example, New York Times fashion critic Vanessa Friedman said the technique would eventually lead to ‘print-it-yourself’ tools for shoppers.
“[…] it will happen, and it will create a dramatic change in how we think both about intellectual property and how things are in the supply chain,” Friedman said.
“Certainly some of the fabrications that brands can use will be dramatically changed by technology.”